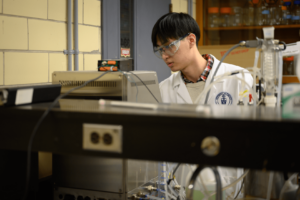
The mining industry in northern Ontario, particularly in Sudbury, has been the economic backbone of this region. As the mining operations generate profits, they also produce large amounts of waste in the form of pyrrhotite tailings, which has become an environmental burden. Under the supervision of Professor Vlad Papangelakis, Heping (Leonardo) Shen (ChemE PhD student) is finding ways to alleviate the economic burden of neutralizing pyrrhotites through a project entitled, nickel recovery from pyrrhotite tailings using a two-step microbially catalyzed process.
“According to 2010 estimates, the total dry weight of pyrrhotite tailings had reached between 50 – 100 million metric tonnes. They are now stored under water, which is more of a containment rather than a treatment. This is not sustainable, as dissolved oxygen in the water will slowly but surely oxidize the buried wastes causing what’s called the acid-mine drainage. During this process, massive acid production will occur, lowering the pH of the water body below 3, which is enough to eliminate almost all living organisms in surrounding ecosystem. An environmentally friendly and economically viable process needs to be developed to ensure the sustainability of the mining operations in this area,” details Shen.
Current treatment of pyrrhotite is associated with enormous costs in neutralization because of the acid production. However, Shen discovered a silver lining!
“A very small amount of nickel (up to 1 wt%) is entrapped in those wastes and recovering this valuable metal could potentially alleviate economic burden. Some acidophilic (acid-loving) microbes like Acidithiobacillus ferrooxidans and can help in the digestion of those solid wastes, liberating the nickel for recovery,” explains Shen.
This is a process called bioleaching, which has several advantages compared to conventional pyrometallurgical (i.e. burning solids) processes. Most notably, it produces no air pollution and requires significantly less energy input.
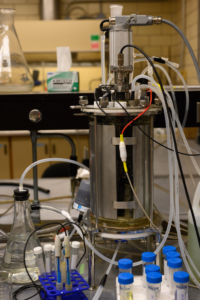
“If we think the pyrrhotite tailings with nickel entrapped as the enemy to be broken apart, then ferric ions (Fe3+) are the soldiers we deploy. Once the enemy (pyrrhotite) is attacked (leaching), our soldiers are sadly spent … together with freshly released iron from the pyrrhotite they become ferrous ion (Fe2+),” analogizes Shen.
“Now is the time for our microbes to shine! Normally in acidic conditions the conversion of ferric ions (Fe3+) to ferrous ion (Fe2+) is extremely slow, but microbes like At. ferrooxidans can greatly accelerate this process, making sure there’s always enough soldiers to attack the enemy. The only problem is that those microbes will also convert released elemental sulfur to sulfuric acid when there’s oxygen, and we want to minimize that,” explains Shen.
Shen’s approach separates the ferric ion attack and the ferric ion regeneration into two steps, removing the released elemental sulfur in between via simple solid-liquid separation. By doing this, his method avoids the mass production of acid and benefits from the accelerated reaction speed from the microbes.
With the growing need for nickel in EV-battery manufacturing and the depletion of high-grade nickel ores on a global scale, the mining industry is turning its eyes to low-grade ores and wastes, like pyrrhotite tailings. The process Shen is developing and the mechanistic understanding he has learned from developing this process compliments this industrial-focus shift, as well as strengthens sustainability of mining operations in northern Ontario.
Shen’s research was conducted in collaboration with fellow ChemE researchers Dazhi Ren, Srinath Garg, and Christine Romano. Their work has been published in the COM2020 proceedings in 2020 and is set to be published at the IBS conference, which will take place at the end of this year. Their project is funded by the Ontario Ministry of Research and Innovation and Ministry of Northern Development and Mines, Genome British Columbia, and NSERC.